Inside an Eco-Friendly Foundry
At Lodge, we’re dedicated to developing comprehensive programs to minimize waste. We ship an average of one million pounds of iron product each week—all melted, poured, molded, finished, and packaged in South Pittsburg, Tennessee. Being a hometown manufacturer helps us operate more efficiently, but that’s only half the story of our eco-focus. Every step of the way, we reuse and recycle materials to reduce our footprint and protect our beautiful home and planet.
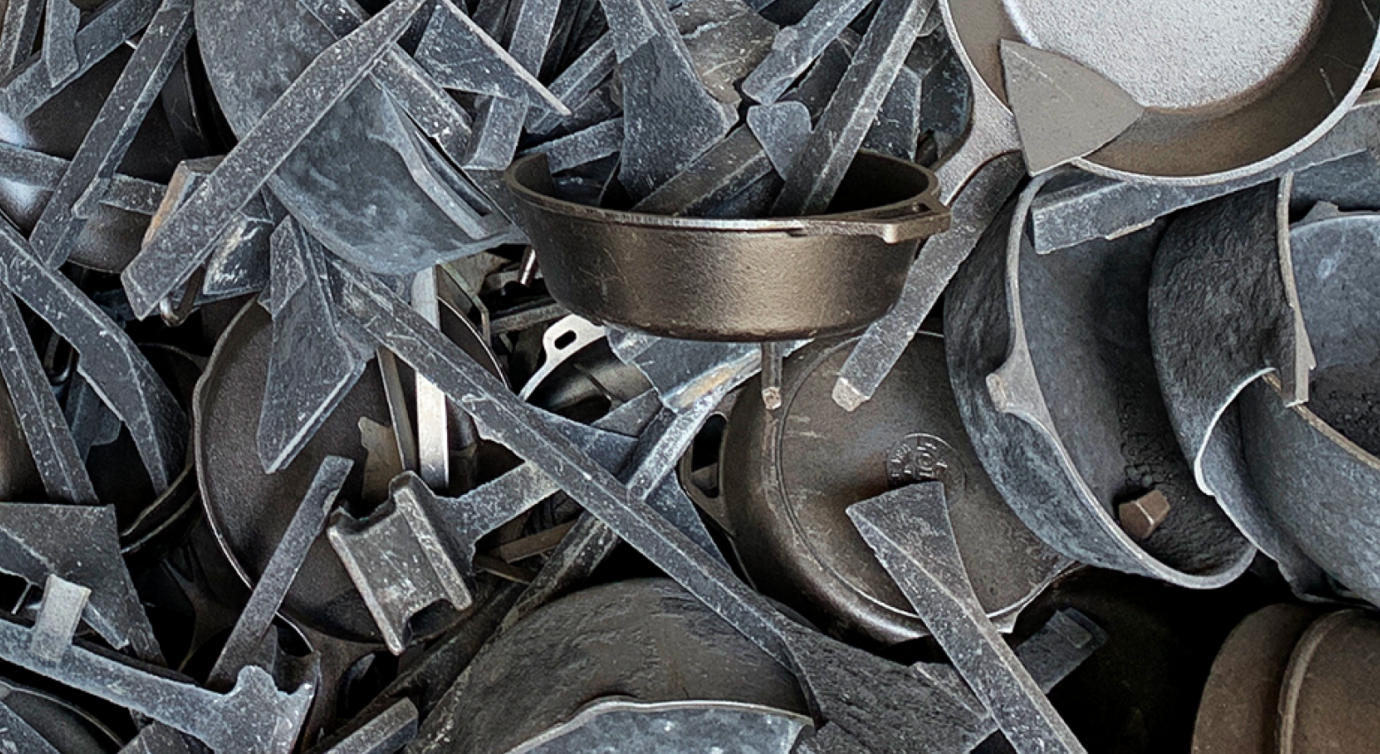
Sourcing Scrap Materials
We mix pig iron, recycled steel, alloys, and castings from our foundry to create the molten iron that makes our heritage cookware. By using recycled steel and scrapped castings, we keep materials out of the landfill. In 2021, we purchased 9,076 tons of recycled steel, or slitter steel, and remelted 33,370 tons of defective castings to keep materials in use for generations.
Repurposing Foundry Sand
Sand is a huge part of our process. In 1996, we worked with the Tennessee Department of Environment and Conservation’s Division of Solid Waste to draft a beneficial use policy for nonhazardous foundry sand. Since then, we’ve repurposed spent sand for construction projects on our campus and in our community, including a baseball field for local kids. In 2021, we recycled about 1,000 cubic yards of spent sand to use on projects around campus.
Recycling Seasoning Oil
One of the final steps in the manufacturing process is seasoning our cookware. Last year, we recycled 15.9 tons of seasoning oil. Instead of disposing of excess oil, it’s reused by other companies to manufacture their products. In fact, a lot of the oil we give away is used in dog food or makeup.
Want to learn more about our environmental initiatives at Lodge? Read the full story →